Pneumatic Air Rams Can Beat the Heat in Steel Mills
Peanut butter and jelly. Batman and Robin. Extreme heat and hydraulic attachments. Two of these three pairs make for classic combinations. Extreme heat and hydraulics, not so much.
In environments like steel mills and foundries, the heat involved with metal processing can go beyond extreme. Temperatures of molten steel can reach 2,500°F (1,370°C) and other metals like aluminum require temperatures of 1,250°F (675°C).
While attachments powered by hydraulic systems can be used for their high force and precision to remove excess slag from smelting pots and molds, they generally can't be used until temperatures dramatically cool. Waiting for temperatures to drop for ladle and furnace cleaning can cause unnecessary delays in steel production, leading to costly downtime.
The challenges with extreme heat and hydraulics can include:
- Hydraulic fluid degradation – high temperatures can cause hydraulic fluid to degrade, reducing its viscosity and leading to decreased lubrication and potential system damage.
- Seal failure – hydraulic seals are susceptible to high temperatures, potentially causing them to harden, crack and leak. Leaking hydraulic fluid can be dangerous in hot steel mill environments, posing slip and fire or explosion risks.
- Overheating – hydraulic breakers themselves can overheat in high-temperature environments, potentially leading to tool breakage or premature failure.
- Dust and contamination – steel mills often involve significant amounts of dust and debris, which can contaminate the hydraulic system and accelerate wear.
A Better Combination
Compressed air and extreme heat are a much better combination. Unlike hydraulic systems that face various challenges in high heat environments, pneumatic systems use compressed air, which is unaffected by heat. Compressed air eliminates the risk of seal failure and hazardous fluid leaks or fluid degradation that can happen with hydraulics, making pneumatic air rams better able to withstand high temperatures—like those found working in steel mills.
Pneumatic air rams harness compressed air to create force and motion, which works well for cleaning tasks that require fast, repetitive movement and moderate force, like removing slag build-up, descaling, or clearing pots.
Ladle Cleaning
Steel ladles carry molten metal from the furnace to the casting area. Over time, slag and refractory debris build up the inside, reducing ladle capacity and thermal efficiency. Pneumatic air rams help clean ladles in a few different ways:
- Slag knock-off systems – air rams with slagger tools or hammers can deliver rapid impact or scraping motion to break off hardened slag from the ladle lip or inner wall.
- Ladle gate mechanism cleaning – rams can actuate cleaning scrapers or rods to clear the sliding gate nozzle area, ensuring smooth operation and preventing metal flow blockages.
- Refractory scraping tools – pneumatic systems can drive tools to remove loose refractory lining after each heat cycle, preparing the ladle for relining or reuse.
Furnace Cleaning
Electric arc furnaces (EAFs) and basic oxygen furnaces (BOFs) accumulate slag and dross on walls, tap holes and spouts. Air rams are used to:
- Clean furnace tapholes – rams drive taphole cleaning rods or drills to clear out solidified slag or metal, ensuring unobstructed flow during tapping.
- Slag door and runner cleaning – rams operate tools that scrape or knock off slag accumulation around furnace slag doors or runners. Their repetitive motion is ideal for automated or remote-controlled slag removal systems.
- Swinging arms or lances – in some setups, air rams are used to extend/retract oxygen or carbon injection lances or swing mechanical arms holding cleaning tools into position.
Pneumatic air rams are also a good alternative to hydraulic systems in some applications because of their safety (less risk in high-temperature areas), ease of maintenance compared to hydraulics in dirty and hot environments (they have fewer seals and simpler construction), and no contamination risk in case of a line rupture (air won't contaminate the steelmaking process).
FRD USA Pneumatic Air Rams

FRD USA is one of very few manufacturers of pneumatic air rams that can be used in the harsh areas of steel mills. The FRD USA B555/B999 AirRam series has proven to be effective for more than two decades on roads and bridges, rock, utility applications, and in steel mills. They are designed for skid-steer loaders, rubber-tired backhoes and excavators.
Features and benefits include:
- Automatic valve provides maximum power with a minimum of air consumption.
- The piston impacts tappet not working steel, protecting the piston from damage.
- Air cushions reduce impact action of piston and tappet reducing wear and tear of critical internal parts.
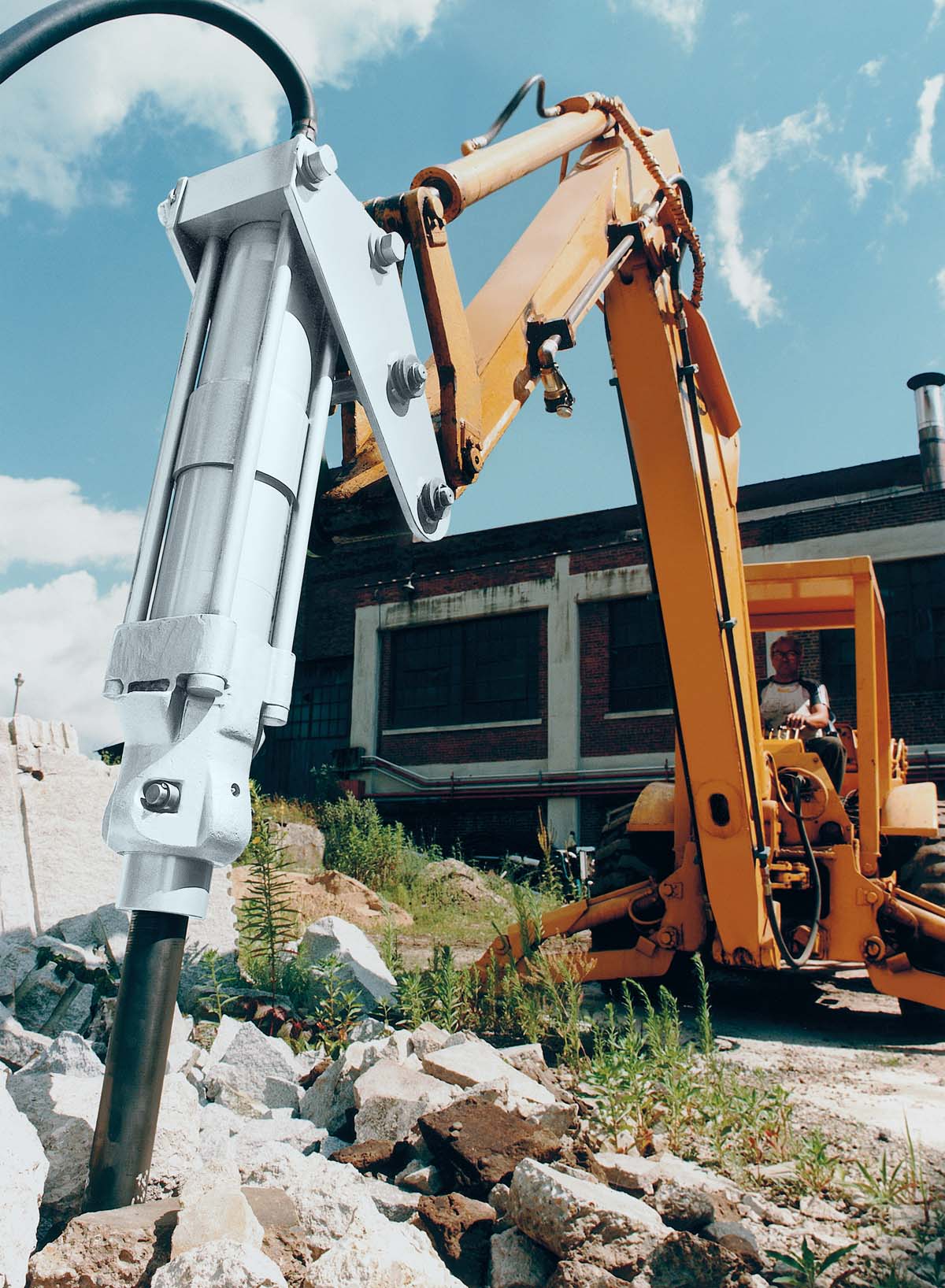