The Important Role Drifters Play in Rock Drills
Rock drills are broadly classified into three types based on the drilling principle: top-hammer drills, down-the-hole (DTH) drills and rotary drills.
In top-hammer and DTH drills, a hammer – known as a drifter – is used to provide percussive force. The primary distinction between the two methods is where the percussive force is placed.
In a top-hammer drill, the drifter is placed at the top of the drill steel, outside the hole. A top-hammer drill has a long rod known as a drill string, which has a bit attached to the bottem end. In the same way as a chisel is hit by a hammer, the top of the drill string is hit by a hammer (the drifter). The drifter transmits cyclical shock waves to the rotating drill bit by applying a percussive force on the drill string, with energy transmitted to the rock in the form of bit penetration – which crushes and pulverizes the rock.
With a DTH drill, the hammer (drifter) literally goes down the hole. A DTH drill has a drill string with a drifter attached to the end, which is located at the bottom of the hole. As the drill string slowly rotates, rock is crushed by directly striking the bit attached to the drifter into the rock.
Drifter Placement
While the placement of the drifter differs with top-hammer and DTH drills, impact is what contributes directly to bedrock crushing. The percussive energy that is generated by the impact is transmitted to the bit in the form of stress waves (particle speed variations). The particle speed variations occur very quickly at the bit tip, allowing the bit to penetrate the rock. For the percussive energy to be reliably transmitted to the bedrock, the bit must stay in contact with the rock, which happens by applying down pressure to the drill string. With both drilling methods, the cuttings are flushed up from the bottom of the hole with pressurized air or water.
Rotary drills, on the other hand, make the bit penetrate the bedrock by quasi-statically pushing the bit into the bedrock without the use of a drifter. A rotary drill applies crushing force to the bit on the end of the drill string, which is pressing into the bedrock.
Top-Hammer Pros and Cons
A top-hammer drill has few size constraints because the drifter is outside the hole. The shape of the piston (hammer) that is in contact with the target bedrock can be optimized to have approximately the same diameter as the drill string, which is ideal from an energy transmission efficiency viewpoint. It is also easy to use hydraulic and other high-power driving sources for the piston. One downside, however, is that the deeper the hole, the more the impact energy weakens as it is being transmitted along the drill string, which tends to lower the performance.
DTH Pros and Cons
Because DTH drills have the drifter located at the bottom of the hole, there are significant size constraints. Compared to a top-hammer drill, the piston diameter must be relatively smaller than the bore-hole diameter.
On the other hand, the drifter (hammer) is located at the bottom of the hole, so it directly impacts the bit. The output remains stable regardless of the depth of the hole, giving DTH drills the advantage over top-hammer drills when drilling deep holes. Also, because the drifter is located at the bottom of the hole, the bore hole diameter, and by extension the drill string diameter, can be wide, allowing for a more rigid drill string resulting in straighter holes, which is also advantageous when drilling deep holes. DTH drilling is most suitable for hole diameters of 4–10 inches, with some exceptions.
FRD Drifters
FRD offers advanced drifter systems designed to drill faster and straighter. The HD 800 Series Drifters provide greater penetration with increased impact. With 20% more impact than its predecessor, the HD 800 Series performs in harder rock and drills larger diameters. Designed around DDS (Dual-Damper System), partnered with a wide range of adjustability for maximum performance regardless of rock.
Learn more about the HD 800 Series drifters here: https://frdusa.com/rock-drill-division/drifters/
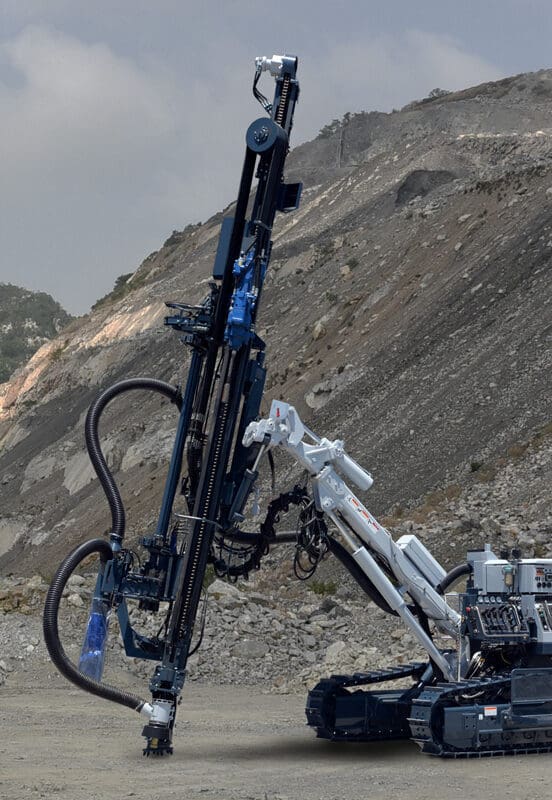