How to Choose the Right Rock Drill for the Job
What’s the best blasthole drill for effective and cost-efficient drilling operations? How can you choose the right rock drill for the job site?
It comes down to asking appropriate questions and working with a dependable partner.
Blasthole drilling – whether top-hammer drilling, down-the-hole or rotary drilling – is primarily used on two job sites: all types of mineral quarries (limestone, granite, talcum, etc.) and construction projects (building new roads, pipelines, running new utility lines).
Drilling and blasting (D&B) impacts many areas of a job site that reach beyond the actual blasthole. There are multiple factors to consider to efficiently reach targeted productivity rates. Those factors include understanding local geological conditions (solid rock, fractured rock, mud seams) choosing the right drilling equipment, climate circumstances, types of explosives required and more.
There are also many technical issues to consider when choosing the right rock drill and drilling method, such as hole diameter, hole depth/bench height, hole angle, special techniques required, legal requirements (dust, noise, etc.). All of these factors will impact the actual cost to drill a hole and the overall D&B operation, but there are three primary factors that drive cost:
- The terrain on the job site (mobility/flexibility)
- The size of the hole that needs to be drilled
- Production—how many feet per day or tonnage per day (for quarries, measured after the blast)
Types of Rock Drills
The three main types of drills are: top-hammer, down-the-hole and rotary. Choosing the type of drill will come from answering the questions above. Here is a brief, high-level explanation of those three types:
- • Top-Hammer Drill – has a long rod known as a drill string to which a bit is attached to the end. In the same way as a chisel is hit by a hammer, the top of the drill string is hit by a hammer known as a drifter, which crushes the rock.
- • Down-The-Hole Drill (DTH) – has a drill string with a hammer attached to the end, which is located at the bottom of the hole. Rock is crushed by directly striking the bit attached to the hammer.
- • Rotary Drill – crushes rock by applying crushing force to the bit on the end of the drill string, which is pressing into the bedrock.
Job Site Considerations
Quarries have fewer variables to consider because they have relatively flat surfaces and relatively known, and consistent conditions. Construction job sites have more variables, requiring the terrain and the mud (overall condition of the site) to be considered, and often drilling a test sample to analyze for mud seams, weathered joints, fractured rock or solid rock to get a picture of what’s being drilled. With that information available, it’s easier to determine the type of drill that is best suited for the conditions.
On construction sites, the top-hammer drilling method is typically used because these types of drilling rigs are smaller and more agile to go more places on uneven terrain. This method is the most suitable for hole diameters between 1–5 inches and hole depths of generally less than 80 feet.
Larger DTH drills are better suited for when the rock analysis identifies mud seams or other challenges with the rock being drilled. These drills deliver a straighter hole, can go deeper than top-hammer drills and are most suitable for hole diameters larger than 4 inches, with some exceptions. DTH drilling rigs are typically larger, but there are some smaller rigs available that are more agile that could be used on construction sites.
Rotary drills are primarily used for large holes (such as coal and limestone) with diameters larger than 8 inches and are better suited for soft and medium-hard rock.
Additional Drill Options
Regardless of the type and size of rock drill chosen, comfort and safety features should be built in, like rollover protection, in-cabin HEPA filters, protection in the cab from noise, and a wide field of vision.
From there, options should be able to be added as wanted or needed to meet application requirements. Some of these add-ons can include:
- Water/dust suppression system
- Remote control
- Cold start kit
- 2 axis angle indicator
- 3 axis angle indicator with length and speed
- Drill monitoring system with GPS capabilities
- Handrails
- Central greasing system
- Back-up camera
- Heavy-duty rear-mounted bumper
Choosing the right rock drill for the job should be based on the conditions of what a job might be and getting a drill that can cover the types of jobs usually done. It starts with answering a number of questions and working with a strong partner to support rock drill equipment over time for long-term success.
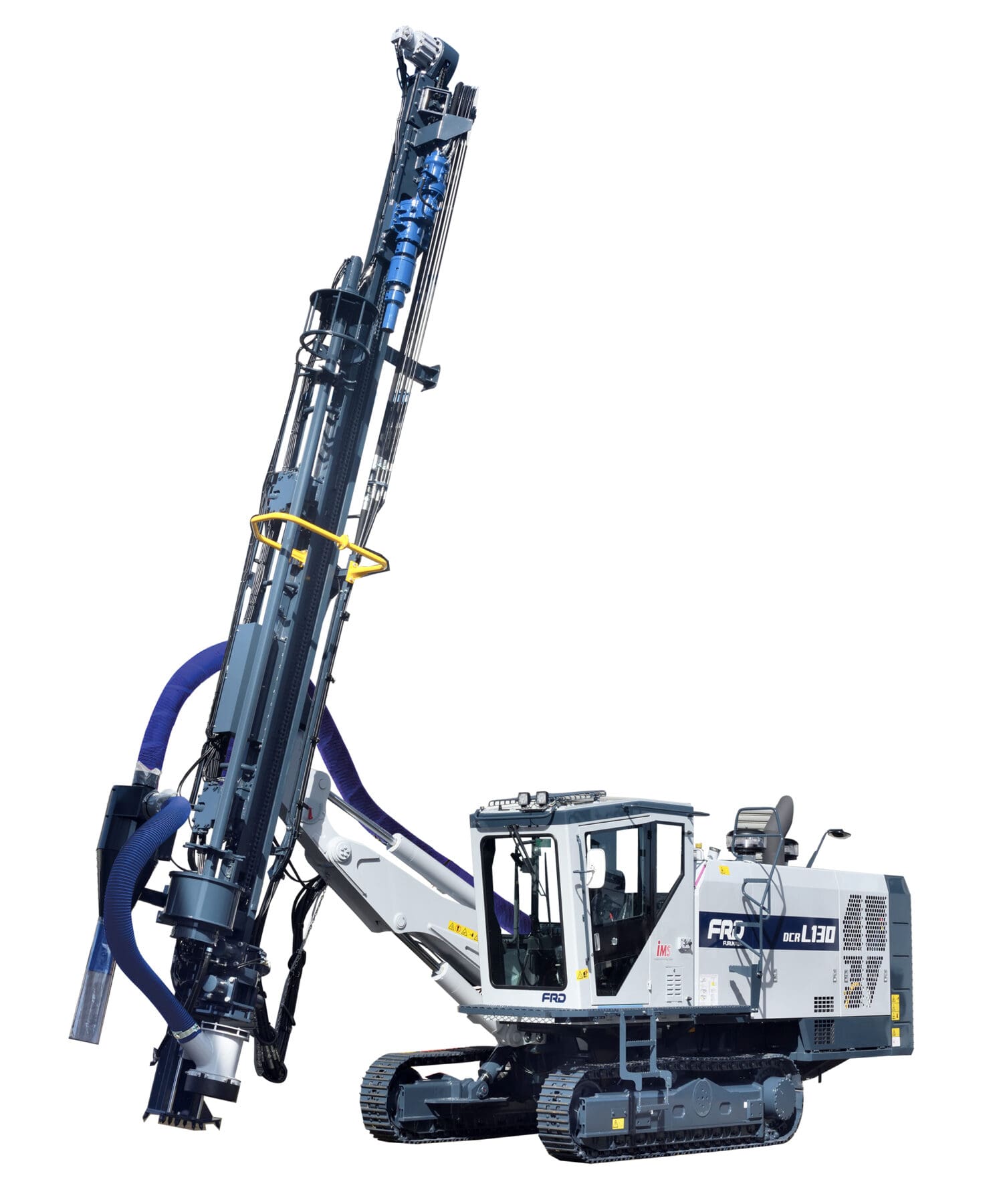